Continuous Improvement (CI)
Continuous improvement is an ongoing effort to improve products, services or processes. It is more of challenging the status quo and looking at opportunities for improved performance. Enables to be competitive in the market.
It is a culture that organization which drives incremental (small) or breakthrough (big) improvements in all business elements.

In 1950's, Toyota implemented small improvement program as part of Toyota Product System. These continual small improvements (Kaizen) and Suggestion Scheme resulted in major benefits.
Realizing the benefits, these small improvement programs have become popular across the world.
And continual improvements have become part of ISO 9001 standard requirements. One has to identify the needs or opportunities and demonstrate the continual improvements year on year.
The projects are identified from results of analysis and evaluation, outputs from management reviews / external audits, customer needs, or bench marking with world class companies for better performance.
While these programs follow Plan-Do-Check-Act cycle at high level, there are different programs/steps to achieve robust solutions for sustainable performance.
One such program, Six Sigma was introduced by Motorola in early 1980's and has 5 phases to achieve defect free outcomes or a set goal. The phases are - Define, Measure, Analyze, Improve, Control.
The typical steps in any Continuous Improvement program include:
- Identifying an opportunity - plus identifying CFT team
- Measure the data - current process performance
- Analyze the data / process - to determine the causes for limited performance
- Develop a solution - to eliminate the root causes and improve the performance
- Implement solution
- Evaluate solution - measure the results for its sustainable performance
- Standardization - standardize process parameters / work practices to ensure gains are sustainable.
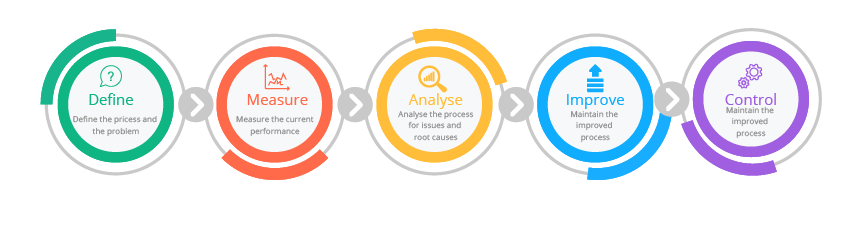
An organization who adopts the continuous improvement for their manufacturing processes will see immeasurable benefits which include:
- Increased productivity
- Improved quality / Zero defects
- Lowered costs
- Faster delivery
- Improved market share
- Greater customer satisfaction